Resource Testing Site Equipped With BiSS UTM-100 kN Universal Machine Was Built At INRTU
INRTU has created a resource testing site as part of the laboratory of digital modeling of technological processes. As part of the federal program “Priority 2030”, the university purchased a BiSS UTM-100 kN universal testing machine fr om India for 24 million rubles.
The site will be headed by Oleg Samoilenko, an assistant of the Department of Technology and Equipment for Machine-Building Production, the winner of the university competition “Young Teacher”.
According to Oleg Samoilenko, the machine will allow INRTU's staff to perform dynamic and static tests of samples or parts made of aluminum, metal alloys, which are carried out to determine a number of mechanical characteristics (elasticity, strength, yield parameters, elongation of the material, etc.).
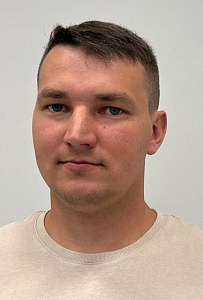
"We chose the BiSS UTM-100 kN machine based on the experience of our Russian colleagues from Novosibirsk and Kazan, wh ere similar equipment has proven itself very well. This turned out to be the most acceptable option under the current sanctions.
The machine will allow us to perform contractual work more efficiently. In addition, it opens up new opportunities for scientific research, as it is important to quickly obtain information about the physical properties of the material.
We will independently assess the impact of the developed technologies on the durability of parts and obtain input data on the material for modeling since this machine can conduct material testing according to GOST 1497-84 and GOST 25.503-97.
The BiSS UTM-100 kN will be integrated into the overall equipment complex, and we plan to actively cooperate with the composite materials section," commented Oleg Samoilenko.
The head of the site emphasized that there is a high demand from customers for durability testing. Therefore, the INRTU team will soon undergo the process of accrediting the new site and machine with Rosaviatsiya to perform certified tests.
The equipment setup and training of INRTU staff were handled by Anton Kuzmin, a representative of the supplier company "Inteltest." Oleg Samoilenko, Alexander Pashkov, and Nikolai Chashchin completed the training.
Andrei Pashkov, Director of the School of Aircraft Construction, Mechanical Engineering and Transport at INRTU, clarified that the university is currently closely collaborating with the National Institute of Aviation Technologies (NIAT), with the customer being JSC Yakovlev. The presence of the laboratory at the university, whose task is to model the technological process and determine its optimal mode, helps strengthen this cooperation.
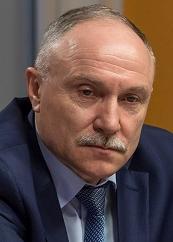
"In aircraft manufacturing, some processes negatively affect the durability characteristics of materials, reducing their cyclic longevity. For example, a process like riveting has not been widely studied. It is good for certain types of parts and improves their characteristics, but at the same time, it creates tensile stress in the metal and reduces the number of cycles before cracks appear. Such things need to be combined with other processes, such as hardening. We plan to test samples primarily for our research tasks.
In addition, we are creating and selling equipment for riveting parts to customers, and we need to provide recommendations on processing modes to prevent a reduction in durability," explained Andrei Pashkov.
He also noted that while JSC Yakovlev previously relied on foreign durability centers, this is now impossible:
"As a result, the demand for these types of work has increased. In a similar laboratory in Kazan, they are evaluating the resistance of structures to cyclic loads. However, no one in Russia researches the impact of technological processes. Therefore, we plan to focus on this area of research and provide customers with a comprehensive approach. Everyone understands that it's not only important to design something, but also to produce a high-quality, durable aircraft that should have a flight time of 60 thousand hours."