INRTU Hands Over the Helicopter Hatch Production Equipment Printed on the Screw 3D Printer, to the Customer
INRTU employees used screw 3D printing technology to create a large-scale tooling for manufacturing a composite cargo hatch for the Mi-171AZ helicopter. The 3D-printed plastic mold has a greater resource compared to molds made of wood-based materials and is much cheaper than that made of metal. The customer was the Additive Solutions (an “Enterprise Aerotech” company, Ulan-Ude).
The work was carried out by the team of the Digital Technologies for Polymer Composite Products Manufacturing research laboratory. The new technological equipment was created thanks to the 3D printing screw extruder purchased under the Priority 2030 program. The equipment was installed on the KUKA robot complex.
According to the laboratory's head, Yuriy Ivanov, the peculiarity of the 3D-printed equipment is that it is hollow inside, so its mass is much smaller than that of a classic technological equipment.
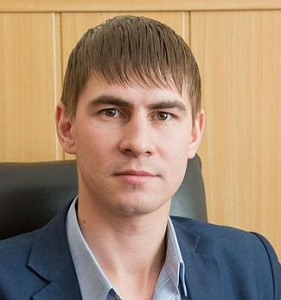
"The customer gave us the parameters, we did the research and adapted existing tooling models for 3D printing. We printed a large mold at an angle to minimize the effect of internal stresses on the part shape. The mold was built with an allowance and then milled.
Although our plastic tooling weighs about 100 kg, it is easier to transport it than, say, a metal one. It is also more resistant to moisture than the wood-based molds.
Compared to metal molds, the new tooling is much cheaper, and compared to wooden molds, it has a longer service life. If you can remove 5-10 parts from a wooden mold (then it needs to be repaired or replaced), ours will last at least 50 cycles," Yuriy Ivanov specified the advantages of the new technology.
Printing was carried out by laboratory engineer Anton Sturov and postgraduate student Lev Shemetov. Master student Konstantin Zenin was involved in the development of control programs, and milling was performed by Evgeny Semenov.
"We have successfully developed the technology for the large-scale mold production, and in the near future the prototype will be delivered to the customer. The plant will use this tooling to produce fiberglass hinged hatches for further installing on the helicopter. We hope that the production tests will confirm the economic viability of the proposed technology," Yuriy Ivanov said.Photos by INRTU Press Service